Page Not Found
We apologize, but the page you requested is currently unavailable. The link may be broken or the content might no longer exist.
Peertechz offers researchers access to millions of scientific documents, including Journals, e-Books, Manuscript Guidelines and Submit Manuscript.
Why not begin your search at our homepage
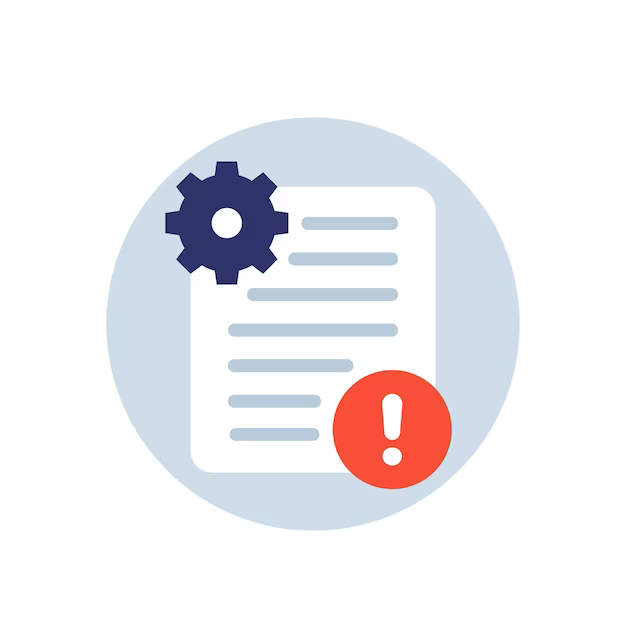